Just In Time Analysis
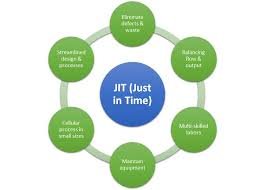
Just-in-time (JIT) inventory management is a strategy that can have significant advantages for companies, but it also comes with its own set of challenges. Here’s a breakdown of a JIT analysis to consider both sides.
Advantages of JIT:
- Reduced Inventory Costs: Holding less inventory frees up capital and reduces storage, insurance, and handling costs.
- Increased Efficiency: Minimizes waste from overproduction and encourages a focus on streamlining processes.
- Improved Quality: Emphasis on receiving high-quality materials from reliable suppliers reduces defects and rework.
- Enhanced Flexibility: Allows quicker adaptation to changes in demand due to lower inventory levels.
- Increased Cash Flow: Faster inventory turnover translates to quicker conversion of raw materials into saleable products.
Disadvantages of JIT:
- Disruptions are Costly: Production halts due to supplier delays, quality issues, or machine breakdowns can be very disruptive.
- Requires Strong Supplier Relationships: Reliance on timely deliveries necessitates dependable and high-quality suppliers.
- Limited Buffer: Little room for error with minimal safety stock, making the system vulnerable to unexpected changes in demand.
- Increased Management Complexity: More coordination is needed between production, purchasing, and suppliers.
- Potential for Employee Stress: Pressure to maintain high quality and efficiency can lead to employee stress.
There isn’t a single specific type of analysis designed solely for Just-in-Time (JIT) inventory management. However, there are several existing analytical approaches that can be applied to assess the suitability of JIT for a company and evaluate its ongoing effectiveness. Here are a couple of relevant methods:
Cost-Benefit Analysis: This is a general framework that can be applied to JIT to weigh the potential cost savings and efficiency gains against the potential risks and implementation challenges. You would analyze factors like:
- Potential reduction in inventory holding costs
- Potential impact on production costs due to potential disruptions
- Potential improvements in quality and efficiency
- Costs associated with implementing and managing JIT systems
Supply Chain Risk Assessment: This analysis focuses on evaluating the vulnerabilities within your supplier network that could disrupt a JIT system. Here, you would assess:
- Reliability of your suppliers in terms of on-time delivery and quality
- Lead times for materials and potential disruptions
- Backup plans in case of supplier issues.
The main objectives of a Just-in-Time (JIT) analysis can be categorized into two main areas:
1. Determining Suitability of JIT:
- Assess company readiness: This involves evaluating a company’s internal capabilities to adopt JIT. It analyzes factors like production flexibility, workforce skills, quality control processes, and management commitment.
- Identify potential risks: Analyzes potential challenges associated with JIT implementation, such as disruptions from unreliable suppliers, limited buffer stock, and increased management complexity.
- Forecast cost-benefits: Estimates the potential cost savings from reduced inventory and potential cost increases due to disruptions or quality issues.
By analyzing these factors, a JIT analysis helps a company decide if their operations and supply chain are suitable for the just-in-time approach.
2. Evaluating Ongoing JIT Effectiveness:
- Measure inventory performance: Tracks metrics like inventory turnover rate and stockholding costs to assess if JIT is achieving its goal of minimizing inventory.
- Identify improvement areas: Analyzes areas where the JIT system can be further optimized, such as streamlining supplier deliveries or improving quality control processes.
- Monitor supplier performance: Tracks supplier on-time delivery rates and quality performance to identify potential weaknesses in the JIT system.
The core concepts of Just-in-Time (JIT) analysis revolve around understanding the trade-offs between efficiency and risk associated with a JIT inventory management system. Here’s a breakdown of the key ideas:
1. Focus on Minimizing Waste:
- JIT analysis centers around the core JIT principle of eliminating waste in all its forms. This includes waste from overproduction, unnecessary inventory holding, defects, and waiting times.
2. Optimizing Inventory Levels:
- A central concept is analyzing the optimal level of inventory to hold. The goal is to minimize inventory carrying costs while ensuring enough materials are available to avoid production stoppages.
3. Supplier Relationships:
- JIT analysis recognizes the critical role of strong supplier relationships. It emphasizes evaluating supplier reliability in terms of on-time delivery, quality, and responsiveness to changes in demand.
4. Continuous Improvement:
- The philosophy of continuous improvement is a core concept. Analysis helps identify areas for improvement within the JIT system, such as streamlining processes, reducing lead times, and enhancing quality control.
5. Cost-Benefit Trade-Offs:
- A core concept is carefully weighing the potential cost savings from reduced inventory against the potential risks of disruptions and quality issues. Analysis helps predict these trade-offs.
6. Risk Management:
- JIT analysis assesses potential risks associated with a JIT system, such as disruptions from supplier delays, quality problems, or unexpected demand fluctuations. It helps develop mitigation strategies.
7. Flexibility and Adaptability:
- A JIT system requires a certain level of flexibility and adaptability within the production process. Analysis assesses a company’s ability to respond to changes in demand or unexpected events.
8. Data-Driven Decision Making:
- Effective JIT analysis relies on relevant data to measure performance and identify improvement opportunities. This data can include inventory levels, production costs, supplier performance metrics, and quality control data.