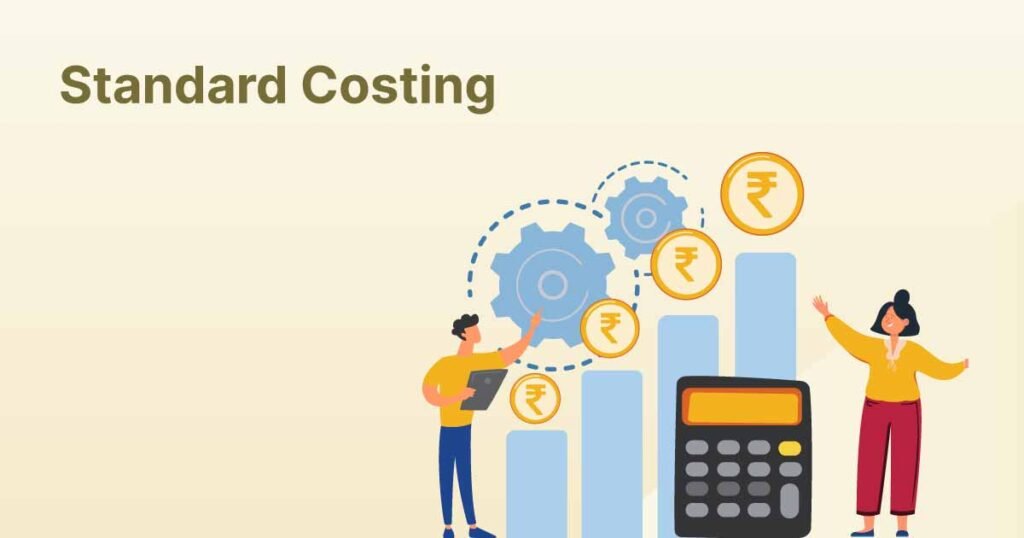
Standard Costing
Standard costing is a method used in cost accounting to track variances between predetermined costs (standards) and actual costs incurred during production. It’s essentially a way to set benchmarks for what things should cost and then compare those benchmarks to what they actually cost.
The core concepts of standard costing revolve around setting benchmarks (standards) for production costs and then analyzing the deviations from those benchmarks. Here’s a breakdown of the key ideas:
Predetermined Costs (Standards): This is the foundation of standard costing. It involves establishing expected costs for three main areas:
- Direct Material Cost: Standard cost per unit of material needed to produce a good.
- Direct Labor Cost: Standard cost per unit of labor required to produce a good.
- Manufacturing Overhead Cost: Standard cost allocated to each unit of production for indirect costs like rent, utilities, and depreciation.
Actual Costs: As production happens, the actual costs incurred for materials, labor, and overhead are meticulously tracked.
Variance Analysis: This is the heart of standard costing. It involves comparing the predetermined standards with the actual costs incurred. The difference between these two is called a variance. Variances can be:
- Favorable Variance: When the actual cost is lower than the standard cost.
- Unfavorable Variance: When the actual cost is higher than the standard cost.
Management by Exception: Analyzing variances helps pinpoint areas where production deviated from the plan. Managers can then focus on these exceptions for further investigation and corrective action. The goal is to minimize unfavorable variances and identify opportunities for cost savings.
Performance Measurement: Standard costing provides a benchmark to assess how well production aligns with cost objectives. By analyzing variances, managers can evaluate production efficiency and identify areas for improvement.
Standard costing offers several advantages for businesses, particularly those focused on production and cost control. Here are some of the key benefits:
Improved Cost Control: Standard costing shines in its ability to identify variances between expected costs and actual costs. These variances act as red flags, highlighting areas where production deviates from the plan. By investigating unfavorable variances, businesses can identify and address inefficiencies, waste, or unexpected price fluctuations. This allows for corrective actions to be taken, ultimately leading to better cost management.
More Useful Information for Decision Making: Standard costing provides valuable data for informed decision-making. By understanding cost behavior and pinpointing areas of variance, managers can make strategic choices regarding production processes, pricing strategies, and resource allocation. This allows for more data-driven decision making and potentially leads to increased profitability.
Simplified Inventory Management: Standard costing simplifies inventory valuation by assigning a standard cost to each unit of inventory. This eliminates the need to constantly track and update the actual cost of every item, saving time and resources.
Cost Savings in Record-Keeping: Standard costing streamlines record-keeping by using predetermined costs instead of tracking every single material or labor expense in detail. This reduces the workload on accounting teams and allows them to focus on more strategic tasks.
Potential for Production Cost Reductions: By identifying areas of inefficiency through variance analysis, standard costing can pave the way for cost reduction efforts. Businesses can use this information to optimize production processes, negotiate better prices with suppliers, or identify areas where automation can be implemented.
Performance Evaluation: Standard costing provides a benchmark for measuring production performance. By comparing actual costs to standards, managers can assess how well production aligns with cost objectives and identify areas for improvement. This can help motivate employees to achieve better results and contribute to overall production efficiency.
Management by Exception: Standard costing facilitates a “management by exception” approach. Instead of getting bogged down in every detail, managers can focus on the variances that signal potential problems. This allows them to prioritize their efforts and address the most critical issues impacting production costs.