Throughput Accounting
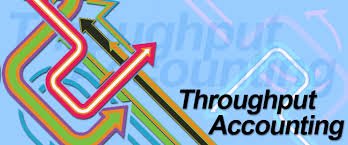
Throughput accounting (TA) is a relatively new approach to management accounting that focuses on maximizing a company’s profitability. It differs from traditional cost accounting methods by emphasizing factors that directly impact a company’s ability to generate profit, rather than focusing solely on minimizing costs.
Here are some potential advantages of using throughput accounting:
- Improved Focus: By emphasizing throughput, TA encourages managers to focus on activities that directly contribute to profitability.
- Enhanced Visibility: Clearer visibility into inventory levels and operating expenses can help identify areas for improvement.
- Simpler Calculations: TA calculations are generally simpler than traditional cost accounting methods.
However, there are also some limitations to consider:
- Limited Cost Analysis: TA provides less detailed cost information compared to traditional methods, which might be less suitable for complex cost structures.
- Applicability Challenges: TA may not be universally applicable to all industries or business models.
- Implementation Complexity: Transitioning from traditional accounting systems to TA can be complex and require a cultural shift within the organization.
The core objectives of throughput accounting (TA) revolve around improving a company’s financial performance through a focus on three key metrics: Throughput (T), Inventory (I), and Operating Expense (OE). Here’s a breakdown of these objectives:
1. Enhance Profitability:
- Maximize Throughput (T): This is the primary objective. Throughput accounting emphasizes maximizing the rate at which the company generates revenue through sales, minus only the variable costs directly tied to production (typically raw materials). By focusing on factors that increase sales or reduce waste, TA helps companies generate more throughput and ultimately, higher profits.
2. Reduce Inventory Levels:
- Minimize Investment (I): TA aims to minimize the amount of capital tied up in inventory (raw materials, work-in-progress, finished goods). This is because excess inventory not only represents idle capital but can also lead to storage costs, obsolescence, and potential waste. TA encourages leaner inventory management practices, freeing up capital for other strategic uses.
3. Improve Short-Term Decision Making:
- Actionable Metrics: TA uses clear and measurable financial metrics like Throughput and Investment. This provides managers with real-time data to make informed short-term decisions. By understanding how their actions impact these metrics, managers can identify areas for improvement and make adjustments to optimize profitability.
Throughput accounting (TA) differs from traditional cost accounting methods in its approach to calculating costs and measuring performance. Here’s a breakdown of the key methods involved in TA:
1. Core Metrics:
Throughput (T): T = Selling price per unit – Variable cost per unit (typically direct material costs). Throughput represents the money a company earns after accounting for the direct costs of producing and selling a unit.
Operating Expense (OE): This refers to all expenses incurred to convert inventory into throughput, excluding variable costs (TVC). OE includes expenses like labor, rent, utilities, and overhead. Unlike traditional methods, most OEs are treated as period costs and expensed in the current accounting period rather than allocated to units of production.
Inventory (I): This represents the total value of a company’s raw materials, work-in-progress, and finished goods. TA encourages minimizing investment in inventory.
2. Performance Measurement:
Throughput Ratio (TPR): This ratio measures the return on investment generated by operating expenses. It’s calculated as Throughput (T) divided by Operating Expense (OE). A higher TPR indicates that the company is generating more throughput for each dollar spent on operating expenses.
Return on Investment (ROI): While not a core metric in TA, ROI can still be used to assess overall financial performance. In TA, ROI can be calculated using Throughput instead of net income, providing a profitability measure based on the throughput generated rather than net profit after all costs are allocated.
3. Short-Term Decision Making:
Focus on Bottlenecks: TA encourages identifying and addressing bottlenecks in the production process. Bottlenecks are any constraints that limit the throughput of the entire system. By focusing on removing or improving bottlenecks, companies can increase their overall throughput generation.
Continuous Improvement: TA promotes a culture of continuous improvement by focusing on measurable metrics. By tracking Throughput, Inventory, and Operating Expenses over time, companies can identify areas for improvement and make data-driven decisions to optimize their performance.
The core concept of throughput accounting (TA) revolves around maximizing a company’s profitability by focusing on throughput, inventory, and operating expense. It represents a significant shift from traditional cost accounting methods that prioritize minimizing overall costs. Here’s a breakdown of the key ideas:
1. Throughput (T): This is the central metric in TA. It represents the cash generated from sales after accounting for the variable costs directly associated with producing and selling a unit (typically the cost of raw materials). Throughput highlights the money a company actually earns, not just the costs it incurs.
2. Inventory (I): This represents the total value of a company’s tied-up capital in raw materials, work-in-progress, and finished goods. A core principle of TA is to minimize investment in inventory. Excess inventory not only reduces available cash but can also lead to storage costs, obsolescence, and potential waste.
3. Operating Expense (OE): This refers to all the expenses a company incurs to convert inventory into throughput, excluding variable costs. This includes expenses like labor, rent, utilities, and overhead. Unlike traditional methods, most operating expenses are treated as period costs and expensed in the current accounting period rather than allocated to units of production. TA argues that focusing on total operating expense reduction can be misleading, as some fixed costs are necessary for basic operations.